Injection Molding
-
国内外の生産拠点で
徹底した一貫生産
金型の研究・開発から成形・加工・組立まで、ワンストップの生産体制によって、お客様から高い評価をいただいている睦月電機のプラスチック成形製造。自動車業界や半導体など高精度で精密、かつ軽量なパーツが求められる現代において、プラスチック成形品の活躍分野はますます広がりを見せています。
私たち睦月電機では、こうした多様なニーズに的確に応えるため、先進プラスチックテクノロジーで、高精度化・小型化・軽量化に取り組んでいます。また、品質・コスト・納期・サービスを意識したモノづくりを心がけ、国内外の生産拠点からお客様のもとにお届けしています。
睦月電機の樹脂成形の特色
製品完成まで全工程をお引き受け、当社で金型設計・製作を実現。
当社1社で管理を行うことにより、工程間に生じる連携ミスを低減。
各部門の納期・品質を一元管理。
ランナーレスシステム(ホットランナー方式)で材料ロスを削減。
土佐山田工場、大阪本社ともに品質保証部門あり。
対応エリアは全国。大阪本社より担当営業がお客様をサポート。
表面処理技術電気制御・設備のスペシャリストが在社。
高知空港から東京・大阪・名古屋・福岡など、主要都市へ飛行機にてアクセス可能。
製品サンプル
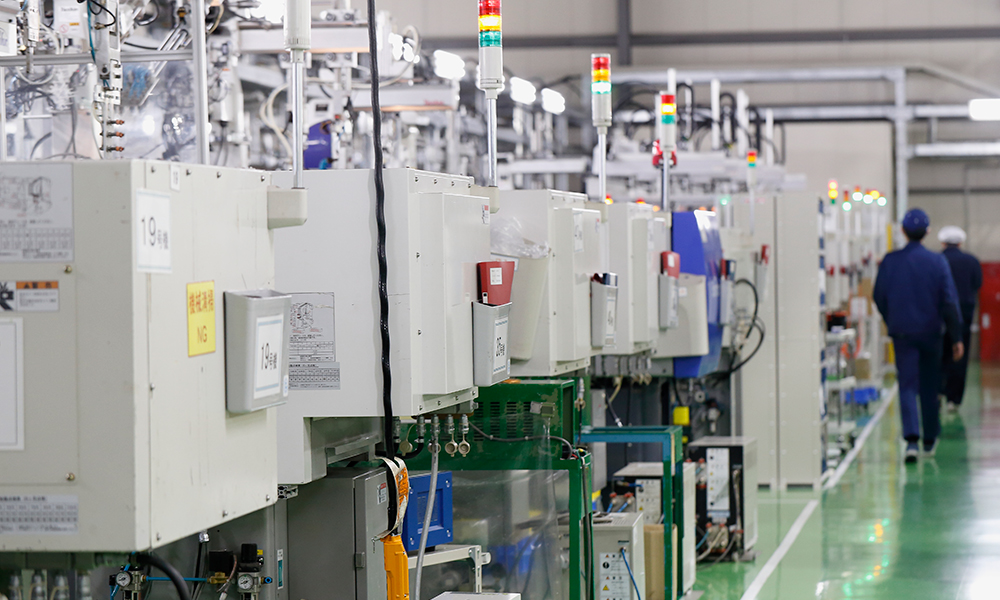
One Stop
高度な金型・射出成形技術をベースにした
樹脂・プラスチック成形をワンストップで提供
生産工程まで見据えたベストな提案
企画・設計
全国に広がるお客様の窓口となる大阪本社。
ここはまた、先端商品の開発の場でもあり、難易度の高いプラスチック成形品の企画から設計を行っています。
当社が採用しているのはランナーレスシステム(ホットランナー方式)。
設計段階から材料費を削減しコストダウンができるよう、ベストな設計を行います。
土佐山田工場の金型製作スタッフとともに、より進んだ金型製作技術、成形加工技術の開発に取り組んでいます。
高度な金型・射出成形技術をベースにした
金型製作
プラスチック成形のポイントは金型です。収縮率を考慮して、製品図面どおりに金型を起こすことは、さほど難しいことではありません。しかし、これだけでは狙いどおりの製品に仕上がりません。
金型製作からスタートした当社では、半世紀以上にわたる実績と経験をベースに、素材選び、構造、研磨、補正などに研鑽を重ね、完成度の高い製品づくりに力を注いでいます。
また、ランナー部の残存樹脂が硬化することなく、次の成形に充填する仕組みにより、材料ロスを最小限にし、効率的な製造プロセスを構築しています。
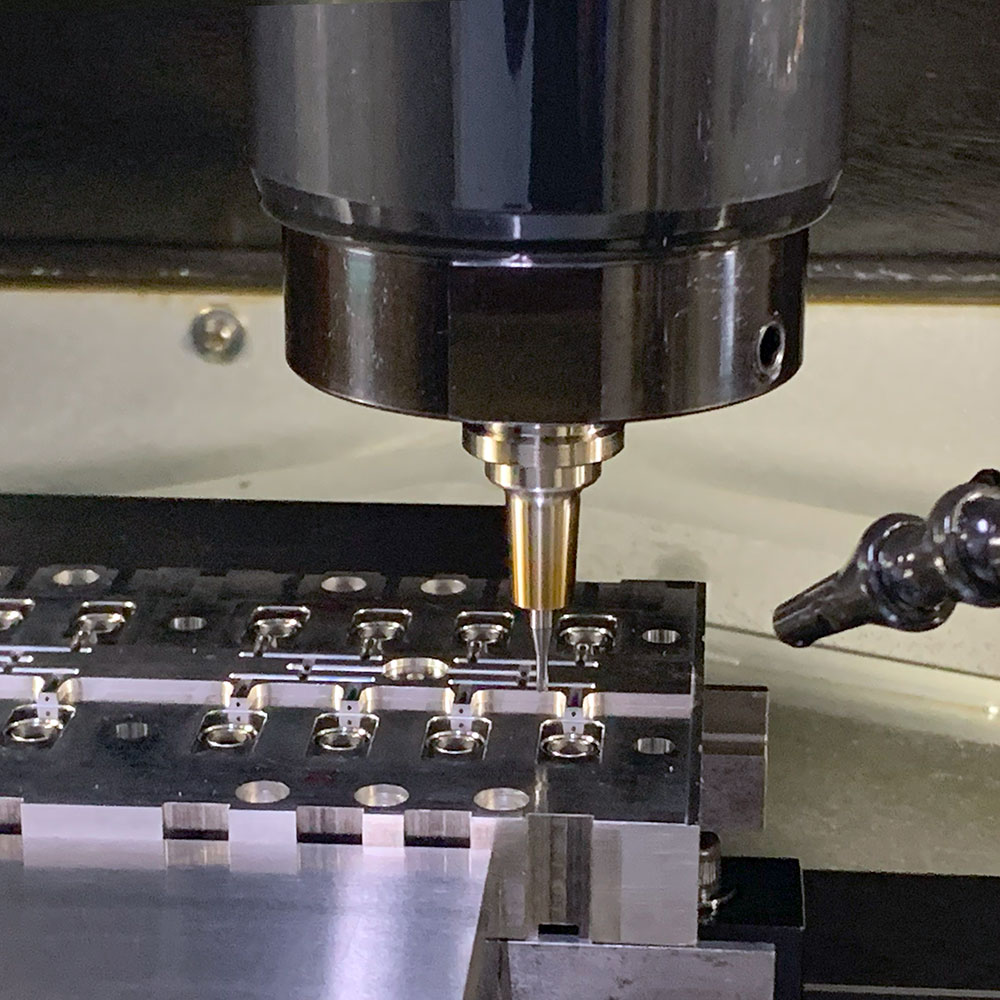
- 超高硬度・特殊鋼をあえて採用
加工が困難なため一般的には用いられないHRC57-63の超高硬度鋼を採用。しかも、焼き入れ後に加工。歪の発生を抑える独自の金型製作工程です。製品精度の向上はもとより、優れた耐久性で高精度を長期間維持。バラツキや不良品の減少にも貢献しています。
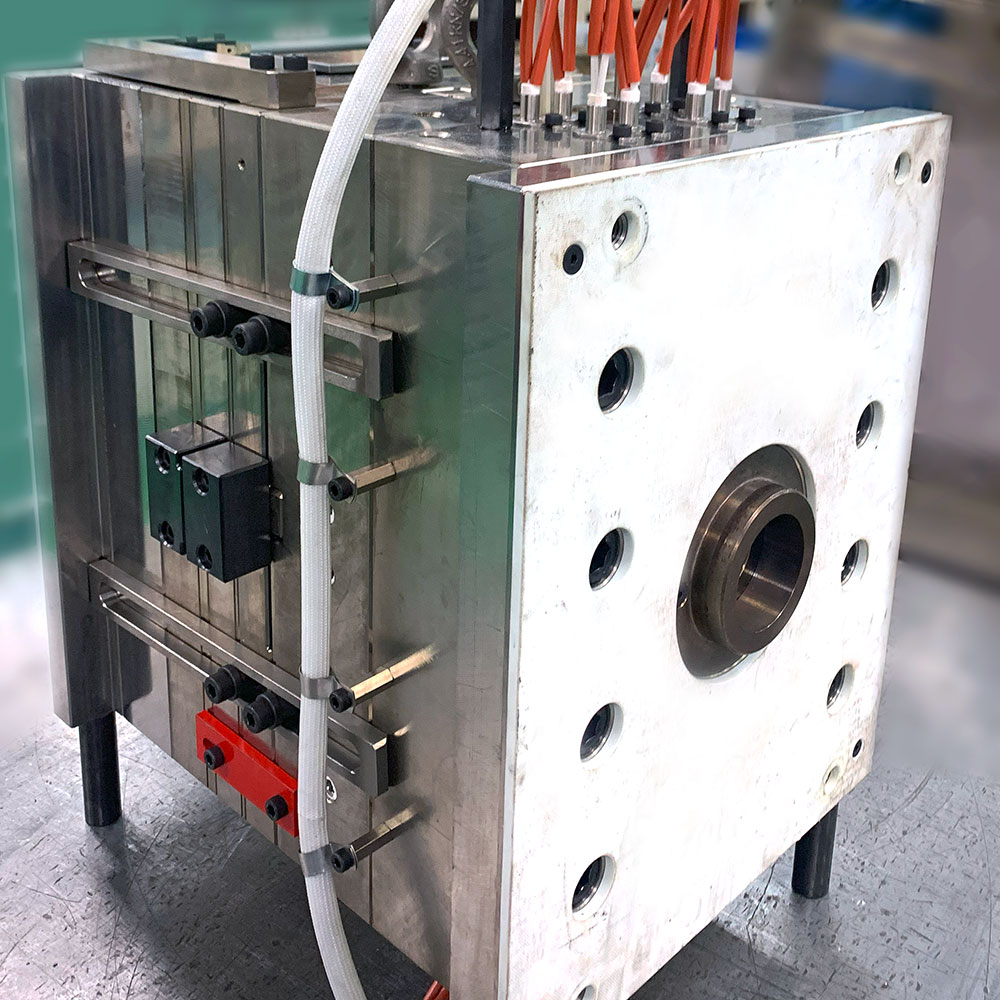
- 高温金型にも対応
高耐熱性、高強度を兼ね備えた樹脂成形を可能にする金型製作を得意としています。金型温度が140~150℃となるPPS、200℃以上となるPEEKといったスーパーエンプラでも、長年培ったノウハウによって、複雑な形状や精密な部品の製造が可能。高温環境においても高品質で安定性のある製品を生み出しています。
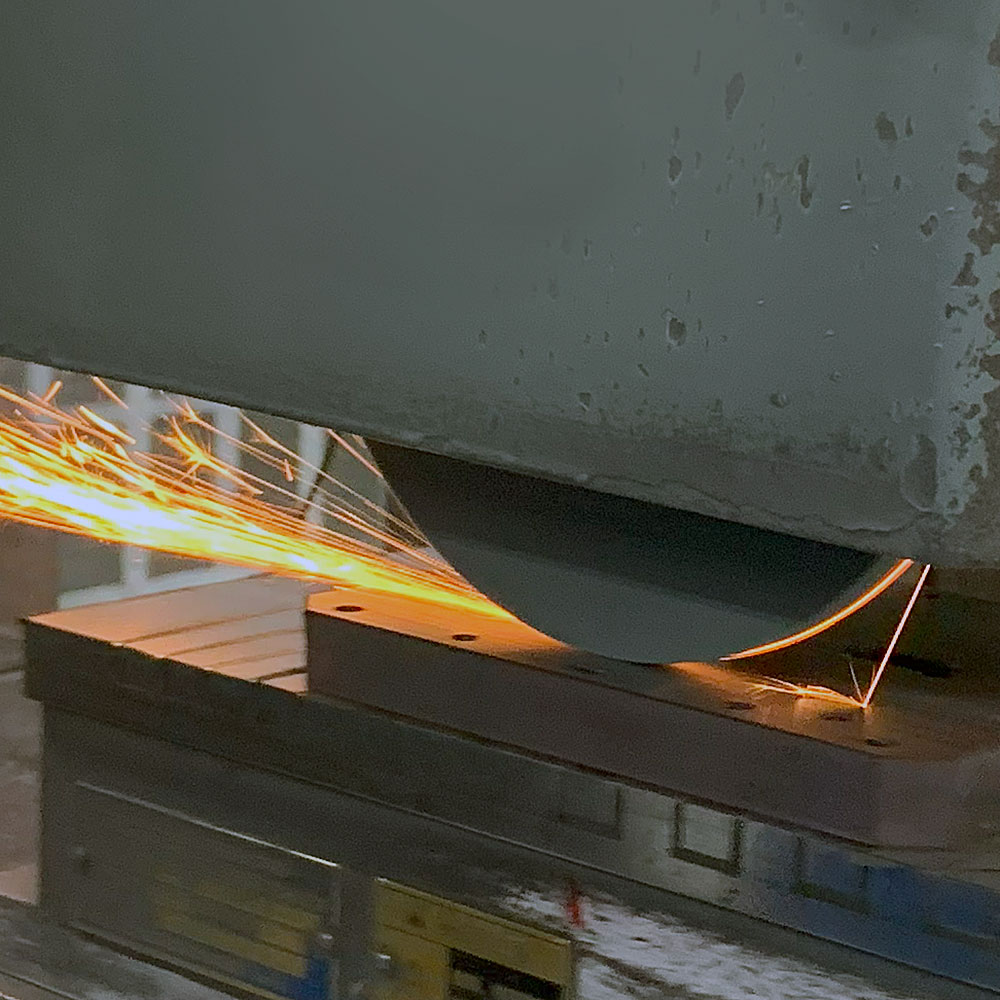
- 入念な補正・フィードバック対応
金型製作には、補正やフィードバックは欠かせない工程です。試験打ちの結果を技術者にフィードバック、研磨などの補正を繰り返し、精度を一段と高めていきます。CAD・CAMだけでは解決できない金型製作の難しさでもあり、豊富な経験やノウハウが求められます。
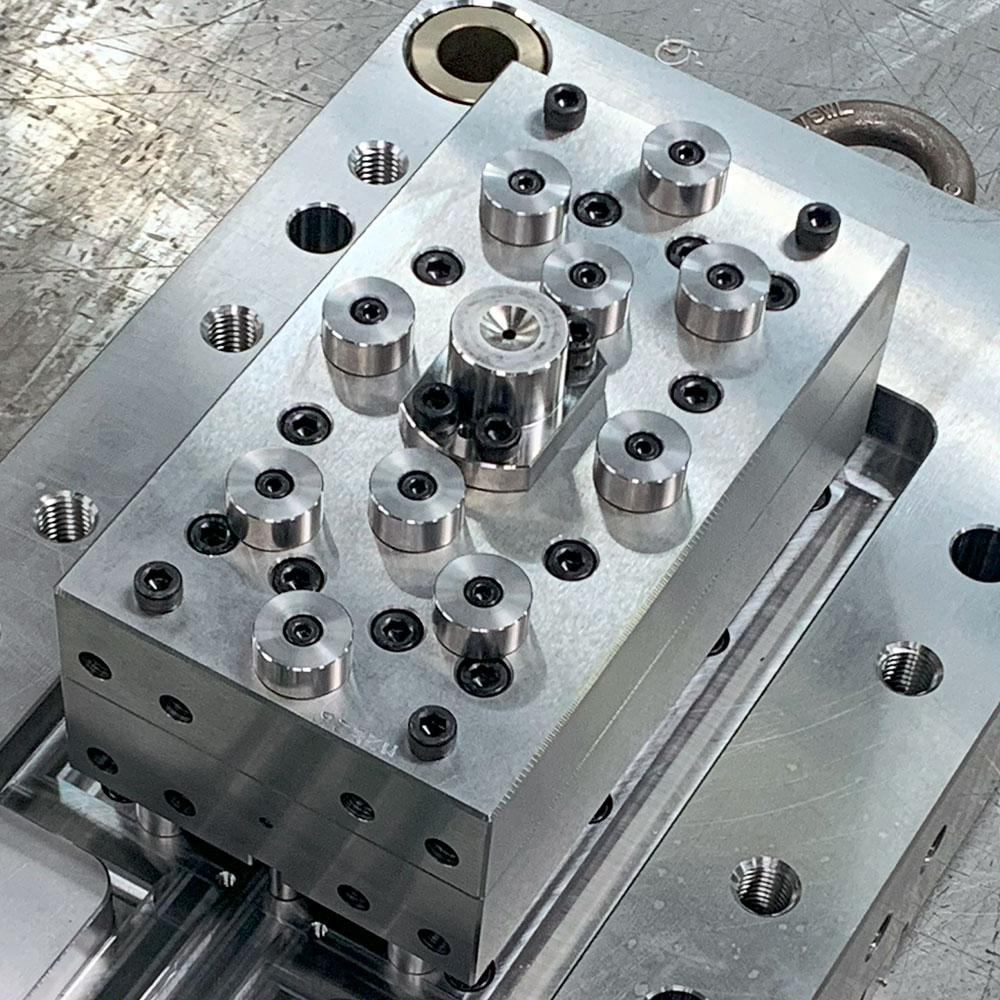
- 独自のホットランナーシステム
当社のホットランナーシステムは、難しい形状の成形品の品質と欠陥のリスクを低減するため独自開発。ランナーレスによって、サイクルタイムを短縮し生産性を向上するとともに、プラスチックの廃棄率を減らし、コスト削減にも貢献します。
小物精密成形が得意分野
成形(二次加工)
PFA、PEEKなどスーパーエンプラと呼ばれる難易度の高い樹脂を用いた、高機能成形品が得意分野。
高知県では最初のインジェクション成形工場として長年培ってきたマン・マシン・マテリアルテクノロジーを武器に、お客様のもとへ高品質商品をお届けします。
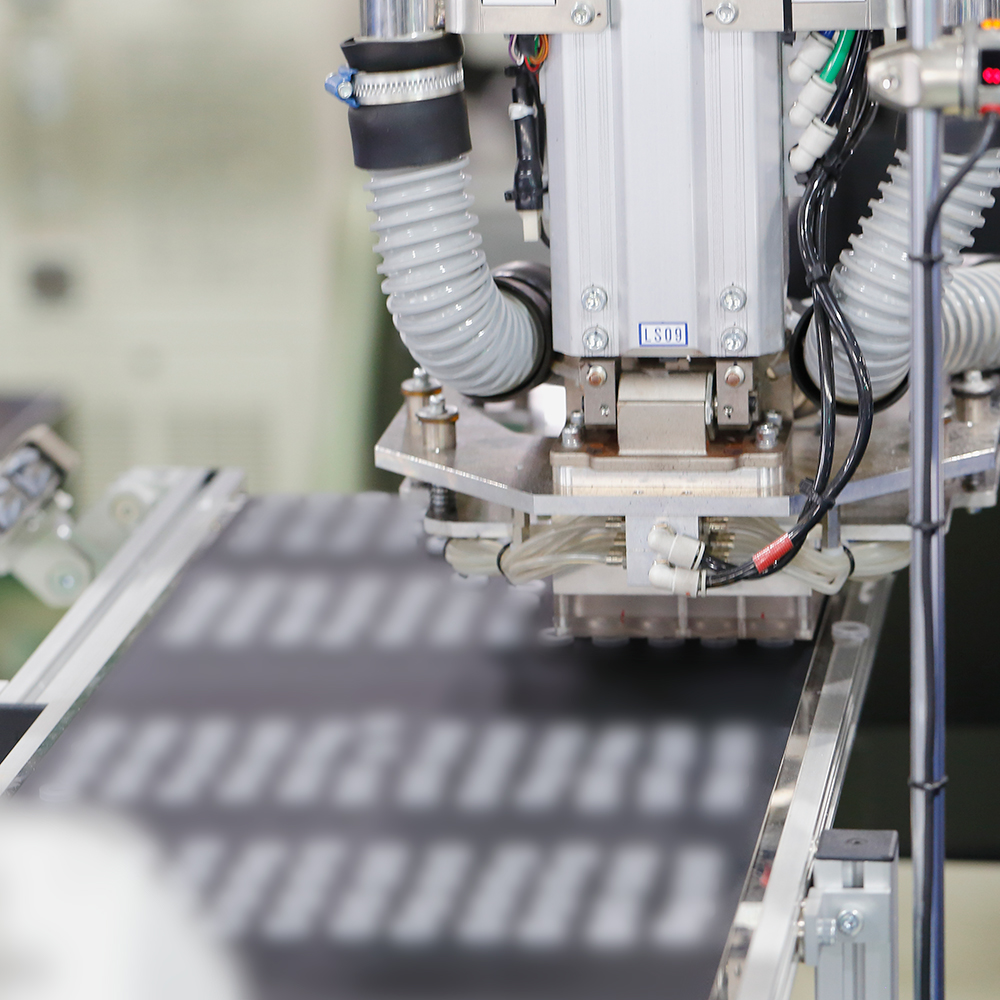
- あくまでも薄く、フラットに
薄く、しかもフラットに。プラスチック成形の苦手な領域です。
この難題に当社は果敢に挑戦してきました。創意工夫を繰り返し確立した樹脂成形技術によって、今や薄肉成形品が必要とされるEV車のモーター部品、FCV車部品の開発、メディカル分野への参入を実現しています。
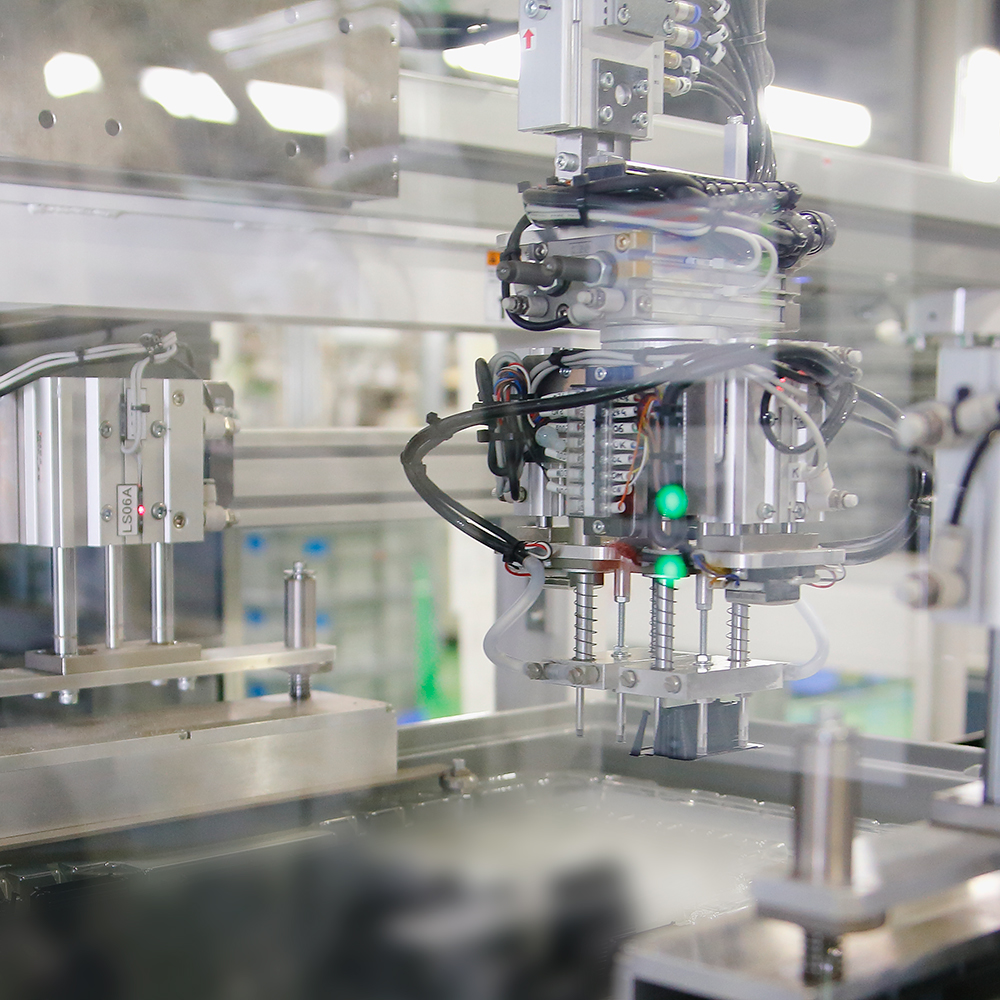
- ダイキャスト並みの精度と強度
超精密度と耐久性が必要なパーツには、従来はアルミダイキャストが採用されていました。この常識を打ち破ったのが当社のプラスチック成形技術。
シビアな金型製作をはじめ、高度な成形技術の確立、より安定した品質管理の要求に応え、プラスチック成形では考えられなかった分野を切り拓いてきました。
画像監視システムや自動検査機を導入
品質管理
自動車業界においては、基準に応じた適正なCPK、SPC管理を実現。
生産数量や製品形状によって画像検査方法をアレンジし、省人化とコストダウンを実現した実績は多数。
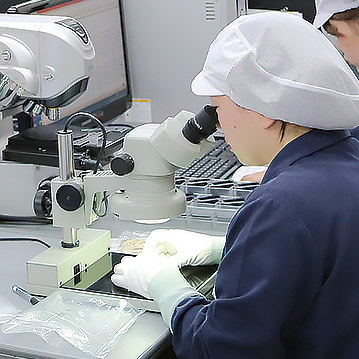
- ベテランによる目視検査も実施
徹底した品質確保のため、目視による全数検査も実施。自動検査機との協働で、品質の安定化を図りながら、高効率稼働でジャスト・イン・タイムの納品にお応えしています。
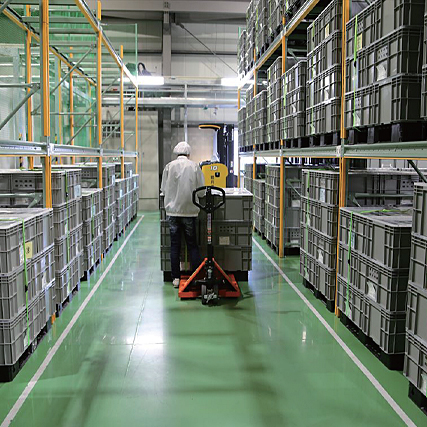
- 綿密な進捗と納期管理を実施
3ヶ月フォーキャストをもとに、PSIを計画、自社工場の成形工程はもちろん、プレス加工やメッキ処理といった強力会社の工程についても、綿密な進捗管理を実施しています。
工法提案
◉スーパーエンプラ(PEEK、PFA など)の豊富な試作、量産経験を活かして樹脂・金属材料形状のご提案が可能
製品設計
◉射出成形、後工程まで見据えた最適提案
◉自社内製のホットランナーシステムで高難度の薄肉成形を実現
金型設計・2次加工仕様決定
◉樹脂特性に合わせ、量産性も考慮
◉要求品質実現に向けコストを意識した後工程をご提案
金型製作・設備製作
◉焼入れ型に自社加工を行なう事でミクロン精度を実現
◉成形を含むライン全体のサイクルを適正化
成形、2次加工条件の最適化
◉プロセスウインドウで成形条件を最適化、各工程でFTA、FMEAなどの手法を活用して故障モードの潰し込みを実施
試作、製品の性能評価
◉製品ごとの要求品質に合わせてフレキシブルな性能評価の実施
◉金型立上げ時の工程能力確認
量産工程
◉重要箇所の傾向管理により変化を見逃さず、不具合を未然に防ぐ
◉製造Lot、成形条件、日報の記録によりトレーサビリティを確保
金属と樹脂の接合技術「ALTIM(アルティム)」